Study on the control of the speed curve of the coiling machine for precision coiling machine
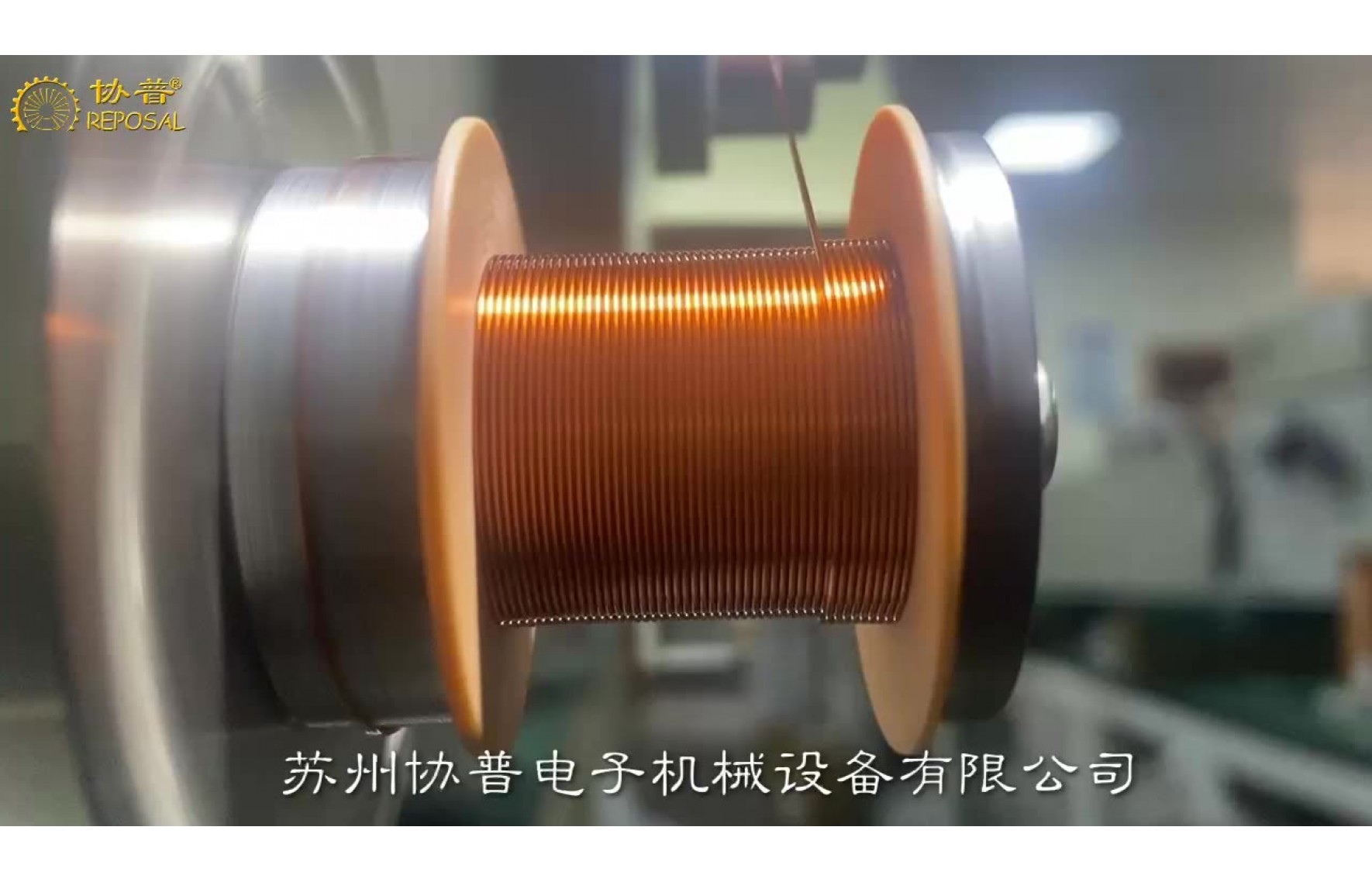
Your factory is using a traditional winding machine, your wire machine structure is reasonable, high mechanical accuracy, the motor is also used a big brand of motor, but in the winding of precision coils, there will be a high defect rate, you carefully analyze before improving various factors - equipment structure, processing accuracy, tooling accuracy, skeleton accuracy, enamel wire quality, tension control, etc. But it still doesn't solve the problem. But to tell you that it's not just a hardware problem, but an algorithm problem, may surprise you. Because in your opinion, every time the spool is transferred, the spool has a corresponding response, but in fact, you may not have considered that in the winding process of the precision coil, the wire guide pin is connected at both ends of the coil, and the sudden change in speed may cause the coil to cross the line and be raised. These defects can degrade the performance of the coil.
To solve this problem, we propose an acceleration and deceleration method based on 5-segment S-curve. The algorithm uses linear acceleration or deceleration at the end and end of the line motion control to help reduce coil defects. We first verify the feasibility of the algorithm by using ADAMS software. The software simulates the motion of the precision winding coil and obtains the velocity curve and displacement curve during the motion. Later, the experimental results show that the method of adopting S-curve in the alignment speed control can reduce the coil defect by up to 50%. This shows that the 5-section S-curve motion control algorithm is a promising method to improve the precision and efficiency of the winding process of electric precision coils. By using this algorithm, coil manufacturers can reduce the risk of coil defects and improve coil performance.
Winding machine is a special production equipment for precision winding coils. They can be divided into stator winding machine, flying fork winding machine, ring winding machine and flat winding machine according to the working mode and object. Different types of equipment are suitable for the production of different objects. For example, the stator winding machine is mainly used to produce motor stator coils, while the parallel winding machine is used to produce electromagnetic switching coils.
Ordinary algorithm of parallel winding machine in the production of precision winding coil products, although our mechanical structure, parts processing accuracy has been done very well, but often there is a problem of low wiring accuracy. In the process of winding a line coil, there are two main movements, one is the rotating movement of the skeleton, which is called winding movement, and the other is the translation movement of the guide needle, which is called wiring movement, and wiring transport is matched with winding movement. After years of technical accumulation, we analyze that the leading role in the alignment accuracy is the alignment movement of the guide needle. Therefore, if you want to improve the alignment accuracy of the coil, you need to optimize the alignment movement of the guide pin.
In fact, we have always believed that the winding machine is equivalent to the lathe in the electrical industry, its importance is self-evident, so for its accuracy, there have been many experts and scholars to study this.
Some people studied the mathematical model of precise alignment based on axial pressure compensation around the axis in the process of alignment. The axial pressure was used to improve the alignment regularity of the coil, and the mathematical model was established according to the analysis of the end point of the coil alignment, which improved the alignment accuracy of the coil.
Some people use the 5-section S-curve control algorithm and the 7-section S-curve control algorithm respectively in the research. In motion control, the 7-section S-curve is more complicated than the 5-section S-curve control. This method has achieved more results in the field of CNC machining, but it is not mature in the field of winding machine.
The tension instability caused by the friction between the enamelled wire and the conductor nozzle during coil winding has been studied, which leads to the uneven wiring of the coil and the breakage of the enamelled wire.
Some people have studied the low efficiency of the winding machine in the traditional winding control because of the inertia error in the process of the winding machine. Instead, the servo motion wiring and the inertia error supplement are used to improve the control efficiency of the winding machine.
PLC control is commonly used in the winding machine wiring control system, through PLC control servo motor can realize the winding machine wiring control, both PLC control stability and high precision servo motor advantages. However, there is a sudden impact of guide pin speed in the coil alignment of parallel winding machine, so it is necessary to further optimize the change of guide pin running speed to improve product quality and the smoothness of wire alignment speed. The S-curve algorithm is a kind of smooth transition of speed in the process of motion, which is often used in machining to solve the problem of breaking the tool caused by speed impact and improve the precision of machining products. In the winding machine, the speed of the guide needle can be changed into an arc smooth transition by controlling the movement track of the guide needle, improving the alignment accuracy and product quality.
To sum up, an algorithm based on 5-segment S-curve motion control is proposed to solve the problem of velocity shock in the process of coil alignment by analyzing the law of coil alignment. ADAMS software is used to simulate the trajectory of the guide pin to verify the feasibility of the algorithm. And the application of the example proves that the 5-section S-shaped curve can effectively solve the phenomenon of crossing and protruding in the process of winding, and improve the precision of winding.
Coil wiring principle
The winding method is flat winding, that is, the enameled wire moves synchronously with the guide pin and always keeps perpendicular to the skeleton during winding. The frame is driven by the winding motor with the guide needle movement, the enameled wire is wound on the skeleton, in which the guide needle is located in the wiring arrangement mechanism and the winding mechanism are two independent mechanisms. The winding mechanism is divided into three stages according to the motion process of the guide pin, namely acceleration and deceleration stage, uniform speed stage and end point return stage. The acceleration and deceleration stage can be divided into two parts: acceleration stage and deceleration stage. In the early stage of the alignment movement, the guide pin speed from zero to uniform speed belongs to the acceleration stage. At the end of the alignment movement, the process of decelerating until the speed reaches zero is a deceleration stage. The middle constant velocity stage is the constant velocity motion stage of the guiding needle. The terminal reentry stage is a process in which the guide needle accelerates backward again after slowing down and stopping. Here we explain:
Acceleration and deceleration stage
In order to arrange the lines evenly, the two movements of guide pin movement and skeleton rotation should meet certain coordination relations during acceleration and deceleration stage. The time for the guide needle to move one diametral width distance must be equal to the time for the skeleton to rotate once, that is, the guide needle to move just one diametral distance when the skeleton rotates once.
Uniform phase
After the guide needle completes the acceleration process, it enters the uniform speed stage, that is, the speed is unchanged in this stage, and the speed of the skeleton and the translation speed of the guide needle both reach the maximum set quota. In this stage, the time for each line diameter of the guide needle to move is equal to the time for the bone frame to rotate one week.
End reentry cline
When the guide needle moves to the end of the skeleton, if the remaining distance is not enough to arrange the enameled wire of the next wire diameter, this time it is necessary to jump out of the current layer of coil for the crossover line, which is called the end return jump. When the end point returns to the jump layer, the current layer can no longer be routed, so it is necessary to jump out of the current layer to the next layer for winding. At this time, the guide needle will continue to move down the wire diameter distance of a enamelled wire after decelerating to the return point, and the guide needle will stop moving to 8 o 'clock, so as to achieve the jump layer. The reentry movement of the guide needle after the jump floor drives the enameled wire to arrange the wire in reverse, and continues the next acceleration and deceleration, uniform speed, and end point rewinding cycle.
The end-point reentry process has an important effect on the alignment accuracy of the coil. Since the guide needle and the coil skeleton are always vertical in the process of wire alignment, and the speed before reentry is reduced from the speed of uniform movement to zero, it just stops at the reentry point, and then the reverse acceleration is carried out again. Therefore, the process before and after the end point reentry can be understood as the reverse movement of the guide needle. The motion characteristics of the end points after reentry into the cline are consistent with those before reentry. This end reentry design does not cause wear and extrusion between the enamelled wire and the skeleton, thus avoiding deformation of the enamelled wire.
In engineering practice, the commonly used motion control algorithms include trapezoidal curve algorithm and S-shaped curve algorithm.
The trapezoidal curve algorithm is relatively easy to realize the motion control, but there is speed change in the process of wiring, which is easy to cause the problem that the wound coil will bulge or cross the line. In the process of motion control, the speed of S-curve algorithm is an arc transition, which can avoid the impact caused by speed sudden change.
Compared with 7-segment S-curve, 5-segment S-curve is more efficient in motion control because the number of control segments is less and the program running time is shorter. At the same time, the smooth transition of speed change is satisfied. Therefore, 5-segment S-curve is used as the guide pin control mode. The 5-section S-shaped curve divides the winding process into five stages: acceleration stage, acceleration and deceleration stage, uniform speed stage, acceleration and deceleration stage.
The winding process should be divided into 5 stages during the winding control. These 5 stages correspond to the acceleration stage, acceleration stage, uniform stage, acceleration stage and deceleration stage of the S-shaped curve respectively. Each stage needs to complete the winding control according to the groove width of the coil skeleton and the acceleration of the coil. If the control process is forced to stop due to external interference factors, the winding will be automatically stopped.
The REPOSAL ? winding machine has been tested on the company's existing mature winder equipment. Among them, the slot width of the coil skeleton is L=30 mm, and the diameter of the enameled wire is 1 mm. The experiment is carried out. The coil products wound before and after the improvement of the control algorithm improve the defects of some protruding and cross-wire in the previous coil products, effectively solve the problems of coil protruding and sag caused by the process of coil wiring, and improve the quality of the coil products.