General technical conditions for parallel winding machine SJ/T 10313—92
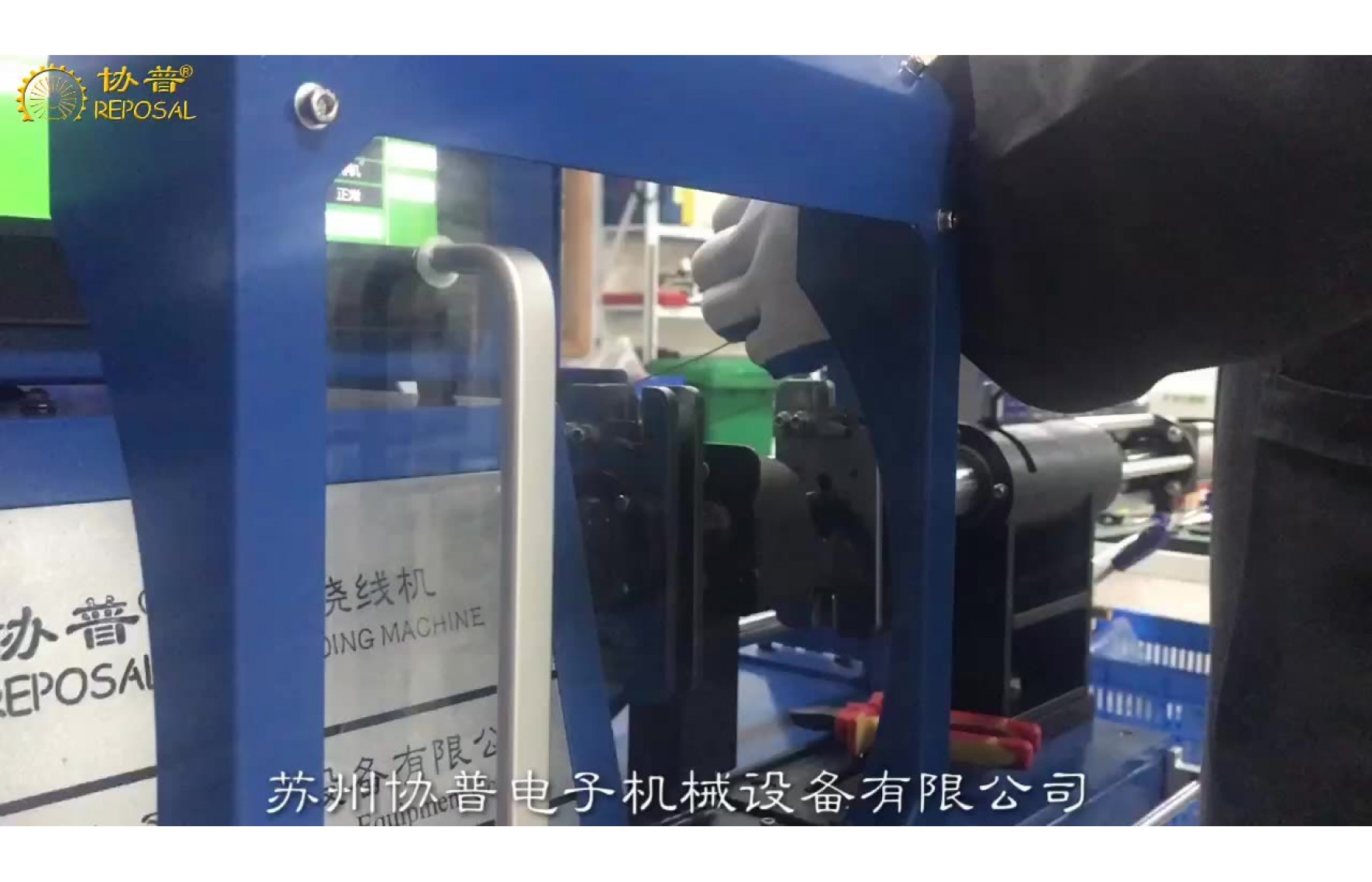
People's Republic of China Electronics Industry Standard
Parallel winding machine general technical conditions sj/t 10313—92
General specification of parallel winding machine
1 Subject content and scope of application
This standard specifies the technical requirements, test methods, inspection rules and markings, packaging, transportation and storage requirements for parallel winding machines.
This standard is applicable to parallel winding machines whose skeleton cross-sectional shape is round or rectangular coils.
This standard does not apply to winding machines for winding ring-shaped, honeycomb-shaped and saddle-shaped coils.
2 reference standards
GB191 packaging, storage and transportation pictorial mark
GB4006.1 winding coil cylindrical bobbin type size
GB4006.2 winding coil tapered coil type size
GB4215 Measurement of noise power level of metal cutting machine tools
GB5080.7 Equipment Reliability Test The verification test plan for failure rate and mean time between failures under the assumption of constant failure rate
GB6109.1 enameled round winding wire part one general regulations
3 technical requirements
3.1 Working condition requirements
Parallel winding machine should be able to work normally under the following conditions:
a. Temperature: 5~38'C;
b. Relative humidity; 20%~65%;
c. Working voltage: 220V±10%.
3.2 performance requirements
3.2.1 Appearance requirements
3.2.1.1 The appearance should be flat, smooth, free from scratches and corrosion, and the plating coating should not fall off.
3.2.1.2 The product label is firmly fixed, the handwriting is neat, and the content is clear and correct.
3.2.1.3 All fasteners should be firm without looseness.
3.2.2 Spindle speed
3.2.2.1 When the spindle speed adopts stepless speed regulation, the speed adjustment should be stable, sensitive, and reliable; when the stepped speed change is adopted, the speed increase and decrease should be smooth.
3.2.2.2 The stability error of the speed should not be greater than 10% of the normal working speed.
3.2.2.3 After the front spindle reaches the preset number of parking turns, the error of the number of turns exceeded due to inertia is not more than 1%, and the parking error of the winding machine with an encoder and indexing function is specified by the product standard.
3.2.3 Cable pitch
3.2.3.1 The wire pitch of the parallel winding machine should be flexibly set according to the diameter of the wire to be wound, and the diameter of the wire should meet the requirements of GB 6109.1.
3.2.3.2 The minimum setting of the cable pitch should be able to reach the thinnest wire diameter wound by the winding machine.
3.2.3.3 The maximum setting of the wire pitch should be 1.1 times the thickest wire diameter wound by the winding machine.
3.2.3.4 The cumulative error of the cable pitch in each layer of winding is not more than 2%.
3.2.3.5 When the cable pitch is set, the uniformity of the pitch is specified by the product standard.
3.2.4 Pay-off device
3.2.4.1 Parallel winding machine should be equipped with corresponding pay-off device, the pay-off device should be able to pay off evenly, and the horizontal pay-off device should have corresponding braking measures.
3.2.4.2 The pay-off device shall have a tension adjustment function adapted to the diameter of the wire being wound.
3. 2. 4. 3 When winding a thin wire with a diameter less than 0.05 mm, the pay-off device shall have the function of disconnection and stop.
3. 2. 4. 4 The pay-off device should match the original spool with the thickest wire diameter wound by the parallel winding machine, and the size of the spool should meet the requirements of GB 4006.1 and GB 4006.2.
3.2.5 Counter
3.2.5.1 The winding machine should be equipped with a turn counter, and the digital display should be clear and easy to observe.
3.2.5.2 The counting of the counter shall be accurate and reliable, and the error shall not exceed 1% of the maximum counting range of the counter.
3.2.5.3 The counter shall have a pre-selection device for preset number of turns and automatic stop at full turns.
3.2.6 Spindle assembly accuracy
3.2.6.1 Spindle radial runout
A. The amount of radial runout near the head of the car is not more than 1 to 2 times the diameter of the thinnest wire wound.
B. The amount of radial runout within the maximum cable length is not more than 2 to 3 times the diameter of the thinnest wire wound.
3.2.6.2 The axial movement of the spindle is not greater than 0.5 to 1 times the diameter of the thinnest wire.
3.2.7 Assembly accuracy of cable arrangement
3. 2. 7.1 Parallel winding machine must have a corresponding wire arranging mechanism. The arranging mechanism shall be equipped with a wire arranging device suitable for the winding dia